Hi Traineebloggen, it’s me Carl, previously just a reader, now a writer.
A little more than a year ago I was a reader of Traineebloggen, but then as a senior in Mechanical Engineering at Chalmers University of Technology in Gothenburg. I had just started to feel a mixture of anxiety and excitement about the future, what do I want to do, with whom and where? And who would want me to do something, somewhere with someone?
Traineebloggen gave me answer to what I want to do (become a trainee), and SKF gave me the possibility to discover new somewheres and someones, so I’ll try to help you guys out, by sharing.
I started as a Global Trainee in Application Engineering, in August of 2017 together with my ten trainee colleagues from across the globe. Would love to tell you more of our intro-month, but Saien and Henry has already got that covered (click here for Henry’s & here for Saien’s posts).
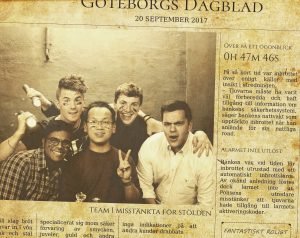
From the intro month: Off work challenge, escape room with Saien, Li, Allan and Dennis.
Clarification of tasks and short description of what I’ve been up to.
Application Engineering: Working very close with the customer to optimize the bearings arrangements. Could be in different phases, either in development phases with Original Equipment Manufacturers, improving current arrangements or root causing failures and prevent them from occurring again. This means that it’s both a strong customer and technical focus. The teams the customer meets consist of Sales, Customer Service and Application Engineering, to be able to cover their needs.
Customer visits: After a couple of years buried in literature, it was really exciting to get out in the real world, at our customers. Sounds pretty cheesy, but working in the engine bay of a towing vessel together with two 37 litres diesel engines was a blast. We conducted service on the drive-train, which included physical inspection of bearings, housing, lubrication and mounting of seals. The service job gave me valuable insight in both the technology and customer relations.
Project: In Sweden, we are set to increase the competitiveness of Swedish industry. Meaning that we need to be in the forefront when it comes to technology, organizational efficiency and being able to deliver the solutions our customers expect. To facilitate for this, several improvement projects are ongoing, and mine is focused on how to increase the value to the customer by having a closer collaboration, and how to set up the business for such a collaboration.
Education: Hybrid bearings in Steyr, Austria. SKF’s site in Steyr develop and manufacture bearings with ceramic rolling elements and coated steel bearings for electric insulation. As an engineer, this is really exciting, since the properties of such bearing are vastly improved in some areas compared to all steel bearings. These bearings are lighter, can run faster, with less lubrication, in more contaminated environments without the risk of being damaged from electrical currents. Meaning that these bearings are the “pièce de résistance”, located in some of the toughest places, such as F1 gearboxes and aerospace applications.
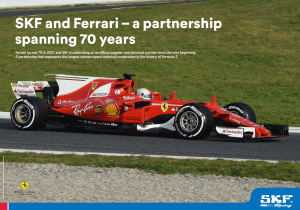
A demanding application and a long collaboration, SKF and Ferrari.
What happens next: In April I’m moving to Brazil for five months, to get to know another part of our global organization. I’m really excited about the journey, since I’m convinced I can contribute to their daily operations and challenges, and also to grow and learn as a global citizen. Hopefully, next time you hear from me, I have more to tell you about this experience.
For you: If you also want to spend 18 months: challenge, learn and develop, both yourself and SKF, apply “here” (for applicants based in Sweden).
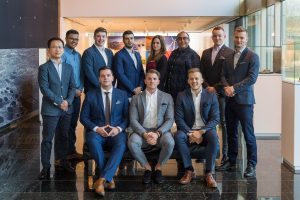
SKF Wave 2 Trainees
If you have any questions, feel free to use the comment section.
Take care!
/Carl
Senaste kommentarerna